Undercarriage rollers for heavy construction equipment are typically manufactured using durable materials to withstand the demanding conditions they encounter.
The specific materials used may vary depending on the manufacturer and the type of roller, but the following materials are commonly used in their construction:
- Steel: Steel is a prevalent material for undercarriage rollers due to its strength and durability. High-quality alloy steel is often used to withstand the heavy loads and abrasive conditions in construction and excavation work.
- Cast Iron: Cast iron can be used for certain types of rollers, particularly in lower-impact applications. Cast iron rollers are known for their hardness and resistance to wear.
- Rubber: Some rollers have a rubber coating or pad on their outer surface to provide better traction and reduce noise. This is often used in road rollers and compactors.
- Polyurethane: Polyurethane rollers are used for applications where a combination of durability and noise reduction is required. They are resistant to abrasion and can provide a quieter operation.
- Plastic: Some lightweight or low-impact rollers may incorporate plastic components to reduce weight and cost.
- Alloy Materials: Various alloys, such as manganese, are used in high-impact and high-abrasion applications to enhance the strength and wear resistance of undercarriage rollers.
- Hardened Steel: For particularly harsh environments, hardened steel is used to increase the rollers’ resistance to wear and extend their lifespan.
The choice of material depends on the specific function of the undercarriage rollers and the type of equipment they are used in. Factors such as load capacity, terrain, and operating conditions all play a role in determining the most suitable material for manufacturing undercarriage rollers. Manufacturers often design rollers with the appropriate material for the intended application to ensure durability and longevity.
What are the signs of wear and damage to undercarriage rollers, and how can they be addressed?
Wear and damage to undercarriage rollers in heavy construction equipment can occur due to the harsh working conditions these machines operate in. Here are common signs of wear and damage to undercarriage rollers and how they can be addressed:
Signs of Wear and Damage:
- Uneven Roller Wear: One of the most common signs is uneven wear on the rollers. Certain rollers may show more wear than others, which can indicate misalignment or damage.
- Excessive Noise: Unusual noises, such as squeaking, grinding, or thumping sounds during equipment operation, can be a sign of worn or damaged rollers.
- Vibration and Shaking: Excessive vibration or shaking of the equipment during operation can indicate problems with the rollers, such as misalignment or wear.
- Reduced Performance: A noticeable decrease in equipment performance, including slower speed, poor maneuverability, or difficulty in maintaining a straight path, China undercarriage rollers may be due to undercarriage roller issues.
- Increased Track Tension: Frequent adjustments to track tension may indicate roller wear, as the need for adjustments increases when the rollers wear down.
- Visual Damage: Inspect the rollers for visible signs of damage, such as cracks, dents, flat spots, or missing pieces.
Addressing Wear and Damage:
- Regular Inspection: Perform routine inspections to detect wear and damage early. Daily or pre-operation checks can help identify issues before they become severe.
- Maintenance Schedule: Adhere to the manufacturer’s recommended maintenance schedule for the equipment, including inspection and maintenance of undercarriage components like rollers.
- Replace Worn Rollers: When rollers are significantly worn or damaged, they should be replaced with new ones. Proper alignment and installation are crucial during replacement.
- Track Alignment: Ensure that the tracks are correctly aligned to prevent uneven wear on the rollers. Misalignment can lead to rapid roller wear.
- Proper Lubrication: Regularly lubricate the rollers according to the manufacturer’s guidelines to reduce friction and minimize wear.
- Correct Track Tension: Maintain proper track tension, which helps distribute the load evenly on the rollers and extends their lifespan.
- Address Root Causes: Investigate and address any underlying issues that may be causing roller wear, such as misalignment, worn sprockets, or issues with other undercarriage components.
- Safety Considerations: When addressing wear and damage, prioritize safety by following the equipment’s safety procedures and using appropriate tools and safety equipment.
If you’re not experienced in heavy equipment maintenance or if the damage is extensive, it’s advisable to consult with a qualified technician or service professional to ensure the work is done safely and effectively. Regular maintenance and prompt addressing of wear and damage are key to extending the lifespan and efficiency of undercarriage rollers.
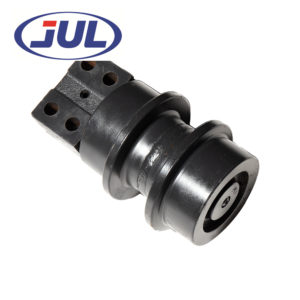