The design of hydraulic pumps can differ from other industrial pump brands in several aspects based on their specific applications and functionalities:
Purpose and Function:
- Hydraulic Energy Conversion: Hydraulic pumps specifically convert mechanical energy into hydraulic energy to power hydraulic systems, unlike other pumps designed for fluid transfer or circulation.
Pressure and Flow Rate:
- High Pressure Handling: Hydraulic pumps are built to handle high pressures, often different from pumps used for lower-pressure fluid transfer.
Construction and Components:
- Precision Components: Hydraulic pumps may have tighter tolerances and precision components due to the need for precise fluid control and power transmission.
Fluid Compatibility:
- Fluid Handling: Designed for compatibility with hydraulic fluids, hydraulic pump supplier considering factors like viscosity, temperature, and pressure variations.
Operating Conditions:
- Diverse Environments: Hydraulic pumps are designed to operate in diverse conditions, from heavy industrial settings to mobile equipment.
Control and Regulation:
- Controlled Output: Often include features for controlled flow or pressure regulation, critical for hydraulic systems’ precise operation.
Power Transmission:
- Mechanical to Hydraulic Energy Conversion: Their primary function is to convert mechanical energy into hydraulic energy for power transmission in hydraulic systems.
Versatility and Adaptability:
- Varied Applications: Hydraulic pumps are adaptable to various applications, offering different types (gear, vane, piston) for specific needs.
Size and Configuration:
- Compact Designs: Hydraulic pumps may be designed for compactness, essential for mobile or space-constrained equipment.
Integration with Hydraulic Systems:
- Seamless Integration: Designed to integrate seamlessly with broader hydraulic systems, ensuring efficient power transmission.
Each industrial pump brand designs its pumps based on the intended application, industry standards, and specific functionalities required by their customers. Hydraulic pump designs prioritize converting mechanical energy into hydraulic power efficiently and precisely controlling fluid flow and pressure within hydraulic systems, distinguishing them from other types of industrial pumps.
Are hydraulic pump designed for high-pressure or high-temperature applications?
Yes, hydraulic pumps are often designed to operate in high-pressure applications, as they are crucial components in hydraulic systems that frequently operate under elevated pressures. These pumps are engineered to handle and generate high hydraulic pressures required for various industrial applications, such as heavy machinery, construction equipment, manufacturing systems, and more.
However, regarding high-temperature applications, hydraulic pumps might have limitations due to the effects of temperature on their components, seals, and hydraulic fluids. While they can tolerate moderate temperatures, excessively high temperatures could potentially affect the performance and longevity of hydraulic pump parts.
Manufacturers may offer specific variations or materials that can withstand higher temperatures, but extreme temperatures might still pose challenges for hydraulic pumps. In such cases, additional cooling systems or specialized designs may be necessary to manage temperature extremes effectively.
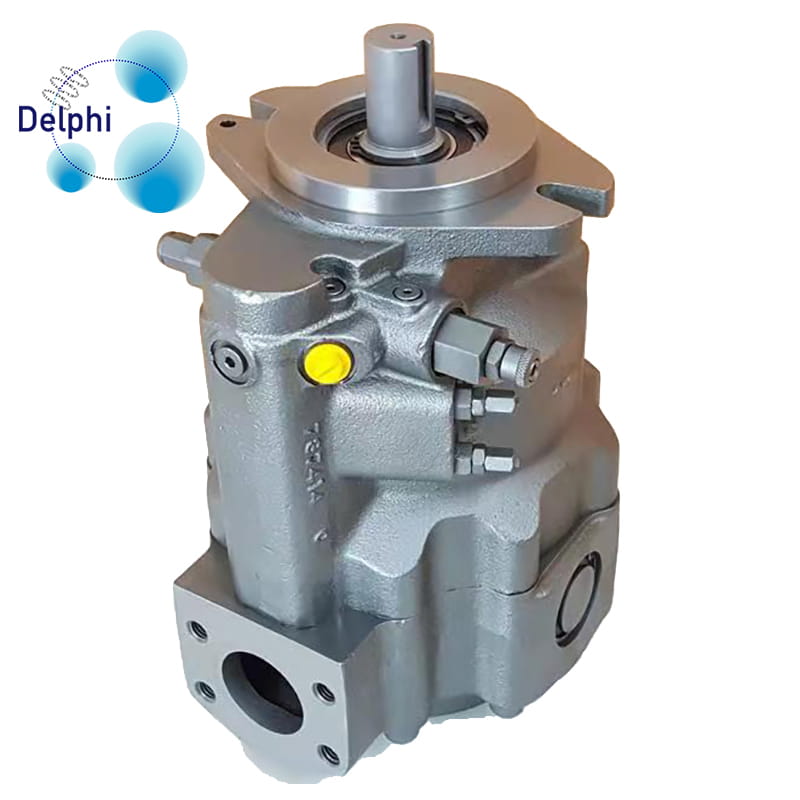